The origins of "Damascus Steel", are somewhat shrouded in mystery, and while there are many theories, the historical accounts that I have been able to piece together seem to indicate that the name came from the location where it was sold (Damascus, Syria). At the time it was viewed a something mystical or magical, simply because the majority of the world was still in the bronze age....and it's performance characteristics surpassed bronze weapons so dramatically.
While many relate "Damascus Steel" to the Japanese and the "Samuri Sword", my personal view of the greatest Bladesmiths throughout history is the Norsemen. Taking nothing away from Japan's contributions to "Damascus Steel", the historical accounts that I have read often speak of the Norse creating multi-bar composite swords, that were so cleverly designed and executed, they were unlike anything of their time.
As man learned more about steel, and how to produce it, the quality gap between mono steels and "Damascus Steel" quickly faded. From my studies, the "Damascus Steel" of old, would be more accurately term "Wootz Steel" in today's terms. Mean while, what we term in modern day as "Damascus Steel", would be more accurately termed as "Pattern Welded Steel"..
I am often asked about "Damascus Steel", and whether or not it is "better" then mono steels in terms of modern cutlery. My response is always the same....It all depends on the Bladesmith. A competent, experienced modern Bladesmith, can produce a Damascus blade that will be no worse, or not better in terms of quality, then the base alloys that the Damascus is produced from. That being said, much knowledge and experience is required on the Bladesmith's part.....there is far more "junk" Damascus being produced today, then ever before. In many cases quality and usability have taken a backseat to eye appeal. In my experience, Damascus is (along with just about every aspect of Bladesmithing/Knifemaking) a "give and take" scenario. For example, to achieve the boldest, most dramatic patterns in the steel, alloys that do not harden may be used.....whereas most alloys that create strong usability in a blade, do not produce outstanding contrast in the finished product. The job of the Bladesmith is to strike a balance between usability and eye appeal. Hence, the "give and take" I previously mentioned.
One major factor that I feel that many miss when trying to produce their own "Damascus Steel", is what I call "compatibility". I use that term to describe the expansion, contraction, and to a degree, the element content within various steel that can be successfully forge welding to produce "Damascus Steel". To explain, to a slight degree, element content difference within each specific steel type often dictates how much is expands when heated, and how much it contracts when cooled. If the attempt is made to join two (or more) steel into a Damascus billet that have widely dissimilar expansion and contraction characteristics, it often leads to failure, or a sub-par quality blade. On the mild side, things such as severe warpage during heat treating occurs, to the Blade literally tearing itself apart when quenched (due to severe differences in expansion/contraction rates the alloys/steels). Part of producing a quality product, is understanding the base materials, and steel is no exception. It is very easy to produce damascus that offers outstanding eye appeal, yet falls far short in terms of usability. It's up to each individual Bladesmith to ensure that what they produce strikes a balance between looking good, and working good. I often use the term "KSO"... meaning Knife Shaped Object to describe much of the junk that some are putting out there.
What do I use? Almost exclusively 1080 or 1084 carbon steel, and and alloy called 15N20. Basically 15N20 is nothing more then 1075 carbon steel, with 1.5% nickel added. When creating Damascus from these materials, they are so similar that all operations, from forge welding through heat treating is very easy, and generally trouble free. And since both alloys have simiar hardening characteristics, they offer outstanding usability in the finished blade(s). And...there are other ways to "color" Damascus to achieve outstanding eye appeal...

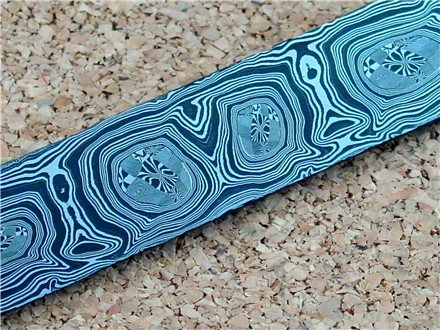
I often produce Damascus Steel for other knifemakers, ranging from simple random and twist patterns, to extoic mosaic damascus. I generally do not keep a large supply of preparted damascus billets on hand, so if you'd like damascus barstock, contact me. Prices vary with the current cost of materials, and the complexity of pattern.
Damascus Steel
(406)727-9102
"Nobody Cares What you Know...
Until They Know You Care!"
Copyright 2024/25: "The Montana Bladesmith"